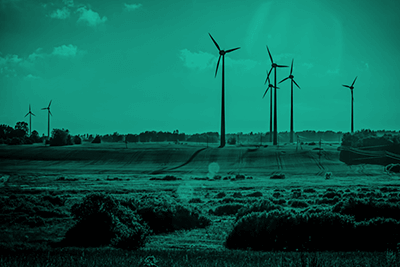
Our Washlines
Regulation Certified Processing: Meeting Strict Wash Requirements
Daniels Mechanical Washsmart technology robotically empties and feeds each Daniels Sharpsmart container through a sophisticated 6-stage washing process.
Using a tested combination of water pressure, heat and biodegradable detergent, our process ensures safe sanitization without the use of harmful chemicals — all while meeting Canadian provincial regulations. Our washing process demonstrates ground-breaking engineering and achieves a 6-log bacterial load reduction, surpassing the sanitization levels of all other container washing methods.