Rome Memorial Hospital
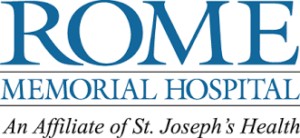
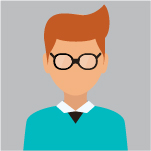
Our Approach
STEP 1
facing and their current “pain points” with the existing vendor and the general safety and wellbeing of their staff. We acquired as much information on the issues as possible to identify the root cause.
STEP 2
The Daniels team conducted a full on-site assessment of the facility and its current waste management practices, observing the current practice of double-stacking biomedical waste bins and the risks it posed to staff, citing container heights in each room, and mapping the movement of waste as it flowed through the facility to identify possible efficiency improvements. As part of the site assessment, we met with each person involved in the management and movement of healthcare waste in the facility to understand their experience, individual pain-points and suggestions for change. This in-depth review of the current program issues helped to frame the solutions required at a full-facility level.
STEP 3
Once all information had been compiled, we put forward a full deployment plan that addressed all of the current safety, cost and operational concerns the hospital was facing. Our submission included not only a proposal for more aptly suited and sized containers to suit volume demand, but also a review of waste-flow within the hospital, remedying container heights to reduce sharps injury risk, implementing an education program to train staff on safer practices and more effective segregation, and setting up the correct processes for the management of each waste stream to ensure compliance. We reviewed our deployment plan with the Rome facilities manager and leadership for approval.
The Results
Let's Talk!
Your time is valuable, and we don’t want to play hard to get. You can either phone us directly on the details listed on our contact page, or feel free to fill out this short form and one of our team members will get back to you as quickly as possible.